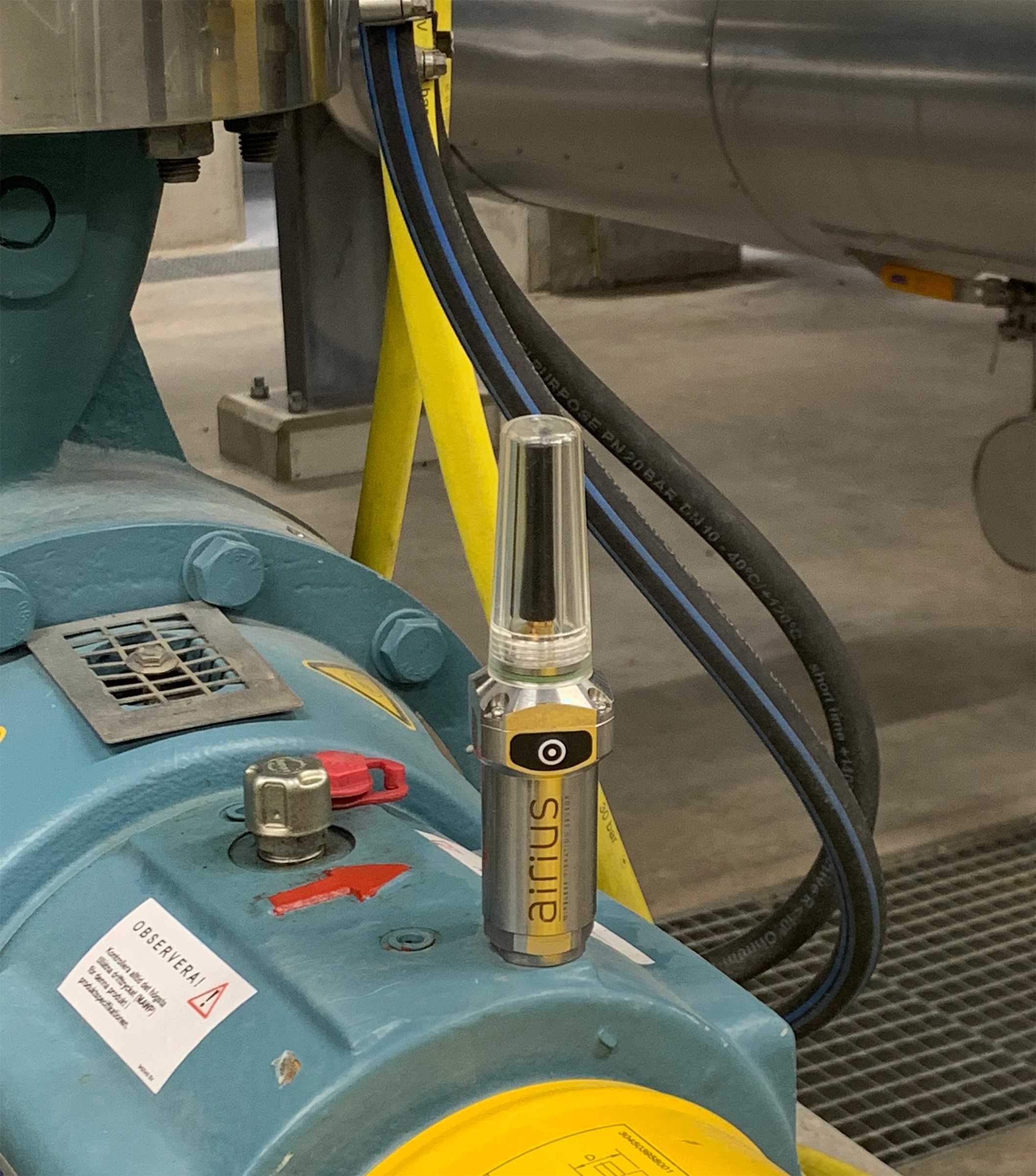
Collaborative innovation: How Södra Cell leverages digitalization with Airius LTE-M wireless vibration sensors
At SPM, we are solution-oriented to the core. Our development work is born out of a genuine passion for solving problems, and a significant part is done in collaboration with our customers. This often involves new software functionality, but sometimes, the result is an extension of our product line. This was the case with our wireless vibration sensor Airius LTE-M, developed at the initiative of our longstanding customer, Swedish forestry company Södra Cell. We sat down for a chat with Thomas Håkansson, Södra Cell’s Head of Technology Development, who approached us in 2019 with a vision of leveraging digitalization technologies to increase the company’s production volumes.
Convinced that interaction between people and technology is the key to increasing productivity and cost-efficiency, Södra Cell embarked on a journey to take advantage of and develop new technology while also incorporating new working methods to leverage the effects of digitalization. Part of this work is pursuing a more fact-based, data-driven maintenance operation. Route-based measurement on thousands of measuring points at each of the three pulp mills was a time-consuming task for Södra Cell’s maintenance engineers. At the same time – due to the sheer number of machines – measurements were not carried out often enough to catch every potential machine problem nor provide enough data for confident decision-making. |
![]() Thomas Håkansson, Head of Technology Development, Södra Cell |
This became the starting point for the idea of replacing manual measurement with automated data acquisition, which would relieve the maintenance engineers and provide an increased amount of machine condition data on which to base maintenance decisions. Online monitoring equipment with considerable amounts of cabling was not a relevant solution because the machines in question are dispersed over large mill areas. Moreover, they do not have the highest criticality rating and, hence, do not require continuous monitoring. Measuring devices with wireless communication thus emerged as the best option.
Bringing suppliers together for mutual benefit
Such a solution would require plant-wide, secure wireless network communication possibilities. But because of the extensive mill areas, building proprietary Wi-Fi networks was not feasible. However, Swedish telecom operator Telia already had cellular base stations installed at all three mills. Södra Cell, therefore, wanted to find out if a wireless vibration sensor might use mobile communication for data transmission and hence reached out to Telia and SPM.
“Working with a Swedish condition monitoring supplier who is both big enough and small enough to be willing to listen to a customer’s ideas is a major advantage for us. So is the fact that the operating responsibility for the wireless communication network rests with the operator,” Håkansson said. “We didn’t want to develop the solution ourselves but set the requirements and have the opportunity to test the product. Here, we benefitted from SPM's knowledge in both the manufacturing and function of sensors and Telia's knowledge in radio technology,” he continued.
At the end of 2019, a decision was made on a joint development effort of a new version of the Airius wireless vibration sensor, which would use Telia's existing infrastructure at each pulp mill to communicate via LTE-M. Barely two years later, the first series-produced sensors were installed. At the time, this was the first wireless vibration sensor with LTE-M communication to hit the market.
LTE-M – a flexible choice for IoT connectivity
In choosing between the NB-IOT and LTE-M radio technology standards, Södra Cell opted for LTE-M – a solid choice for flexible and future-proof IoT connectivity. Advantages include the capacity to send not mere scalar values but spectrums and time signals on every transmission, low latency, and the possibility to update sensor firmware remotely.
However, the chosen technology has its drawbacks. To some extent, LTE-M’s faster transmission capacity comes at the expense of battery life. Achieving the desired battery life of four to five years requires adequate RSSI (received signal strength) values and a specific temperature range.
“The technology works; the current challenge is signal strength and battery life. We can't do anything about the ambient temperature impacting battery life on the sensors installed outdoors. The other cause of battery drainage is that despite the local base stations, signal strength is a problem in some areas of our plants. This is now being reviewed and supplemented for better coverage," said Thomas Håkansson.
Streamlining data acquisition for increased output
The overall purpose of developing a wireless vibration sensor was to achieve higher machine availability and thus increase production – a constant quest in the industry. Södra Cell’s investment in the Airius sensors is weighed against the costs arising in case of breakdown and the cost of manual measurement in terms of time.
With the wireless sensors, measurement currently occurs once a day, enabling the detection of machine faults at an early stage and, hence, the opportunity to plan and carry out maintenance before a breakdown occurs. In this way, Södra Cell obtained a production increase of more than 4,000 tons in the first year alone.
Installed on rotating equipment that is less production-critical, such as screws and pumps, the Airius sensors are a complement to online monitoring, which is used to get more measurement data on critical machines.
Thomas Håkansson said: "We’re using the wireless sensors sort of like a fishing net. It allows us to catch developing problems that we can confirm through supplementary measurements with handheld equipment. The advantage is that we get more measurement data while avoiding our staff having to be near rotating machines. That’s a work environment issue. The downside might be that the measurements are not supplemented by human senses – sight, hearing, smell, etc., which can help give a clue as to whether or not something seems normal."
Södra Cell's vision for the future is that all objects not monitored online will have wireless monitoring, thus allowing the maintenance departments to focus more on objects that may have budding problems. In the long run, Södra Cell anticipates this will enable further reliability improvements.
New roles and collaborative analysis
Thanks to the successful development and implementation of the Airius wireless sensors, Södra Cell has introduced two new roles for data engineers with vibration analysis expertise.
Thomas Håkansson: "Making this project fly isn't just about the technology. When it comes to digitalization, it's about getting technology and people to work together – therein lies the potential. Changed working methods and role distributions have also been a journey for us."
Each mill continues to measure manually on machines not yet equipped with Airius sensors. The two new positions are dedicated to analyzing Airius vibration readings from all three mills. That enables Södra Cell to implement similar working methods in all three plants, increasing competence and developing the area thanks to the increased focus on the vibration analysis part. However, the new data engineers also help analyze data from other SPM measuring systems, and one of the mills has transferred the analysis of online measurements entirely to the central function.
“Route-based measurement is still a significant part of our routines – there are in the order of twelve thousand objects. About two thousand of them are now equipped with Airius sensors, so there are still many objects monitored with manual measurement. We’re trying to establish a collaboration where the routing staff is also involved in analysis and investigations to combine the local knowledge with the central vibration expertise. In the longer term, when measuring routes is no longer done, part of the organizational structure might change – for example, we may need more people to work with analysis and focus more on the knowledge-intensive work,” said Thomas Håkansson. He continued: "We’re on a cultural journey, a transition. The competence that exists centrally should be fully utilized. However, we are not there yet.”
Successful supplier collaboration
Driven by digitalization, the Airius LTE-M development project is a shining example of successful collaboration between Swedish industrial and technology companies.
Thomas Håkansson concluded: "Not all digitalization projects take off and turn into something functional and usable. Many ideas and projects never make it past examples, proof-of-concepts, and testing. In this case, we took our idea to the next step and got it flying together with Telia and SPM, and we are using the solution on a large scale. That makes this development effort stand out from many others. Daring to try something new requires financial strength and a certain amount of courage. We set up new job positions, changed how we work, and believed in this."
So far, Södra Cell has installed and connected approximately two thousand sensors in an even distribution between its three pulp mills. A further one thousand sensors have been ordered and partially delivered.