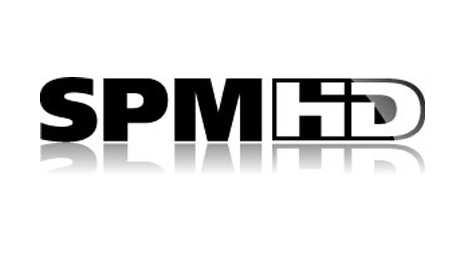
SPM launches revolutionary measuring technique for condition monitoring
In conjunction with the company's 40th anniversary, SPM Instrument AB now presents the next generation of its well-known shock pulse method. SPM HD® is an advanced and patent-pending measuring technique suitable for all types of applications and particularly well suited for low-speed machinery.
Condition monitoring is all about optimizing operations and maintenance to lower costs. The difficulties of getting reliable results when measuring on low-speed applications are a well-known problem. These applications create signals with low energy content, where earlier vibration technologies made it difficult to measure such signals with satisfactory results. The SPM HD® measuring technique combines the well-known and reliable True SPM® method with a highly advanced digital technique. Thanks to its high dynamics, SPM HD® can distinguish the weaker yet relevant signals, which are typically hidden among stronger signals caused by mechanical shock phenomena or electronic noise. The ability to detect very weak signals, therefore, gives decisive advantages when measuring at low speeds. Real-world testing has provided up to six months' forewarning, leaving ample time to plan maintenance and repairs.
The name SPM HD® (High Definition) hints at the extraordinary signal quality as well as a very clear picture of machine condition resulting from the measurements. SPM HD® is built around sophisticated and patent-pending signal processing in several steps. The technique works with digital enveloping of the analog shock pulse transducer signal. The sampling frequency is very high, resulting in a crisp and distinct signal. A 24-bit A/D converter provides razor-sharp resolution and exceptional detail in spectrums and time signals.
For a full picture of bearing condition, the measuring cycle is based on the number of revolutions rather than time. This maximizes the chances of capturing relevant signals in the course of one measuring cycle. By adjusting the sampling frequency to rpm, spectrums are clear and concise.
The measuring technique looks for recurring patterns and uses newly developed and ingenious algorithms to enhance repetitive signals and eliminate randomly occurring high readings. Thanks to the pattern recognition, spectrums and time signals are excellent tools for analysis. The source of the signal is simple to identify, as every component has its own, distinct damage signature. The time signals are easily interpreted, making the type and extent of the damage simple to determine. The benefit of this is no trending is required; occasional measurements provide a reliable diagnosis.
In addition to spectrum and time signal, the measuring technique also generates two scalar values, HDm and HDc. HDm represents the highest value measured during the measuring cycle, while HDc is a measure of bearing lubrication condition. Both values are suitable as the basis for setting alert limits, regardless of machine type. Automatic evaluation of measuring results, presented on a green – yellow – red scale, provides a quick overview of machine condition.
This sophisticated and complete measuring technique is the result of an intense development effort by SPM Instrument and close cooperation with customers in the industry. SPM HD® has been tested successfully on low-speed applications such as twin wire presses, screw presses, drying cylinders and wind turbines, some running at speeds as low as 5 rpm, for many months.
Stefan Lindberg, Managing Director at SPM, comments: "SPM HD® is the unique solution to the problems involving condition measurement on low-speed applications. It sets a new standard for modern condition monitoring and can be used successfully on all types of applications. With SPM HD®, we consolidate our position as a leading supplier of innovative solutions for condition monitoring and predictive maintenance, and we now supplement our successful Intellinova online system with an SPM HD®monitoring unit."