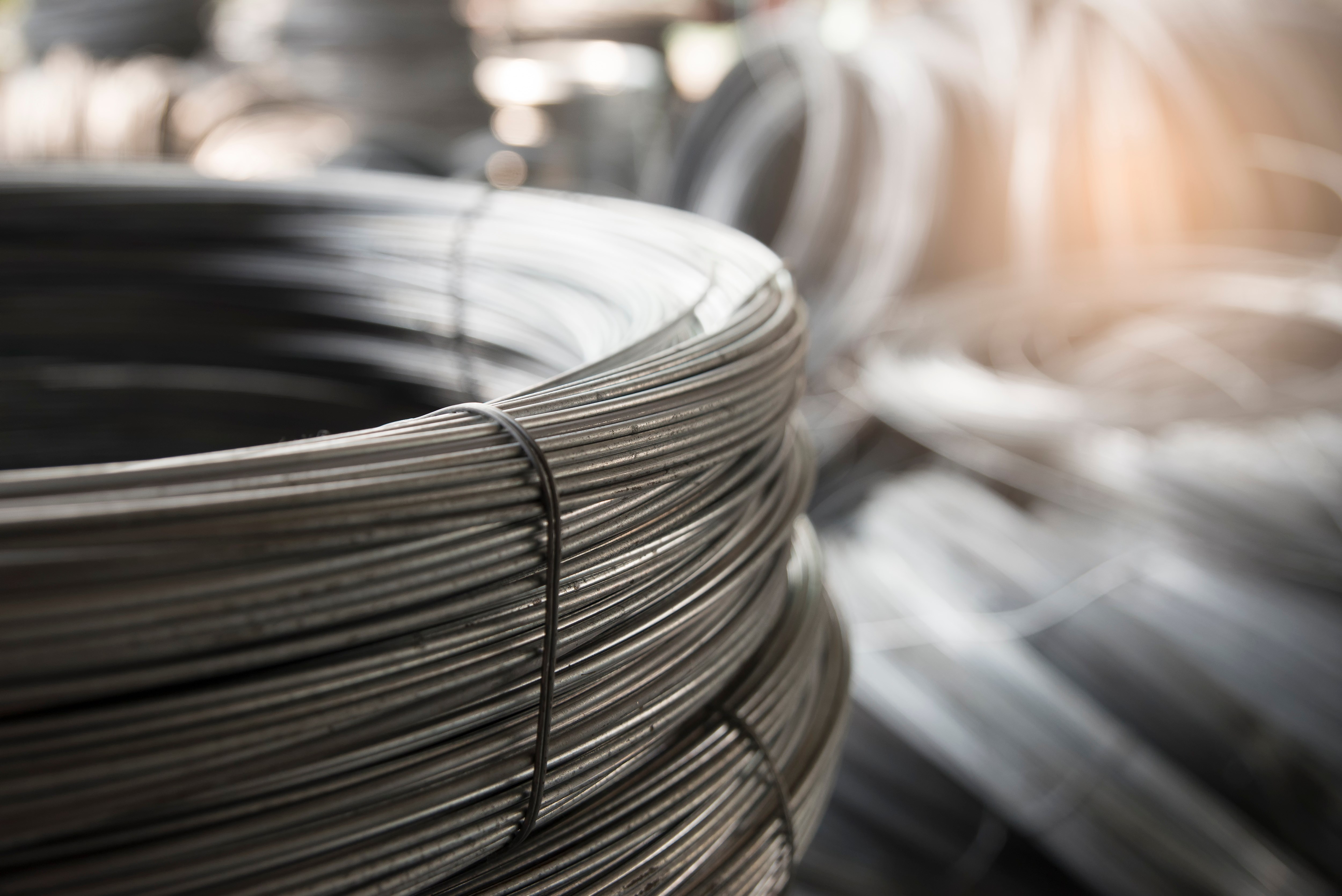
Bearing cage failure in a wire rolling mill
Thanks to its online condition monitoring system, the Austrian steel wire manufacturer averted what could have resulted in significant production stoppage in the nick of time.
The customer's condition monitoring program is designed to detect potential problems early enough to schedule maintenance work for non-productive time. To that end, the plant installed the Intellinova Parallel EN online system with HD measurement technology and DuoTech accelerometers on the gearboxes in its rolling mill.
In December 2022, the online system detected sudden increases in shock pulse and vibration levels corresponding to the FTF symptom. Because of the cage's relative lack of mass and load, the FTF rarely shows up in vibration spectrums until breakdown is imminent – hence, the prewarning time was minimal, making swift action vital. The customer was alerted of the critical time frame and acted accordingly. Without the online system, the broken bearing cage could have resulted in extensive damage to the bearing, gearbox, and auxiliary machines.
When disassembling the gearbox, the damaged bearing cage was confirmed.
The case study is a textbook example of a typical course of this relatively uncommon type of bearing damage.
Download full case study
Case Study
CS036 - Rolling mill gearbox - ATFilename/description | Language | Size | Modified | |
---|---|---|---|---|
CS_036B_Rolling_mill_gearbox_AT.pdf | English (United Kingdom) | 27 MB | 10/6/2023 | |
Case study involving bearing cage failure in a wire rolling mill. | ||||
CS_036C_Rolling_mill_gearbox_AT.pdf | German (Germany) | 27 MB | 1/3/2024 | |
Fallstudie zum Ausfall eines Lagerkäfigs in einem Drahtwalzwerk. |