Power production
The approach to maintenance in the power industry has changed in recent years. Many energy suppliers are now focusing on equipment reliability to strengthen their competitive position and secure a higher return on investments. In a time of shrinking budgets and growing demands, moving beyond conventional maintenance practices becomes a means to an end.
SPM Instrument has been a supplier of innovative solutions for condition monitoring to the power industry for many years. Each sector of the industry has its specific concerns. Safety, reliability, and availability issues influence the growth of the individual power plant as well as the choice of power generation technology and equipment hardware. Common to all is the importance of maintaining availability in production. Interruptions of the power supply cause high costs to the end-user and often a liability to penalties on the part of the distributor. Also, exchanging spare parts can be very costly.
For various reasons, parts of the northern hemisphere are the most power-consuming in the world. For instance, many highly power-consuming industries are located here (such as aluminium and steel plants and paper and pulp industries). A harsh climate in the northernmost parts also demands effective heating systems in buildings during the cold season of the year.
In response to demands for clean and renewable power, wind farms are emerging around the world, and wind power is now the fastest-growing sector in power generation. Our patented methods have proven particularly valuable for the difficult measuring conditions in wind power. The nuclear power industry, of course, has very strict process guidelines. SPM offers measuring equipment suited to plants where safety and environmental integrity must be ensured. In power plants, the typical applications are turbines, gearboxes, and generators. These are mainly monitored by continuous protection systems. Supporting machinery like cooling pumps and exhaust fans are typically equipped with online measuring systems or are included in periodic round measurements with portable instruments, like Leonova Diamond or Leonova Emerald.
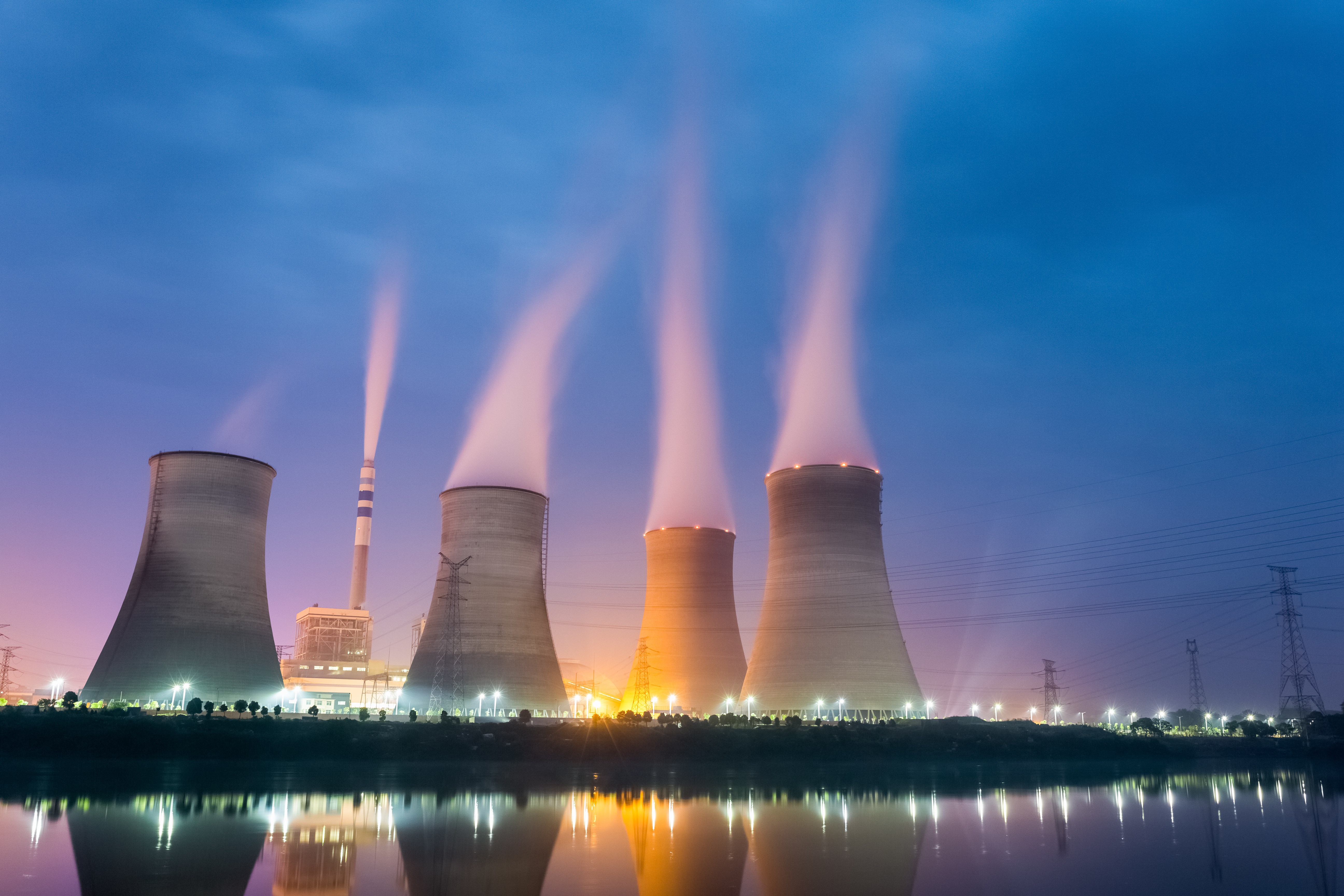
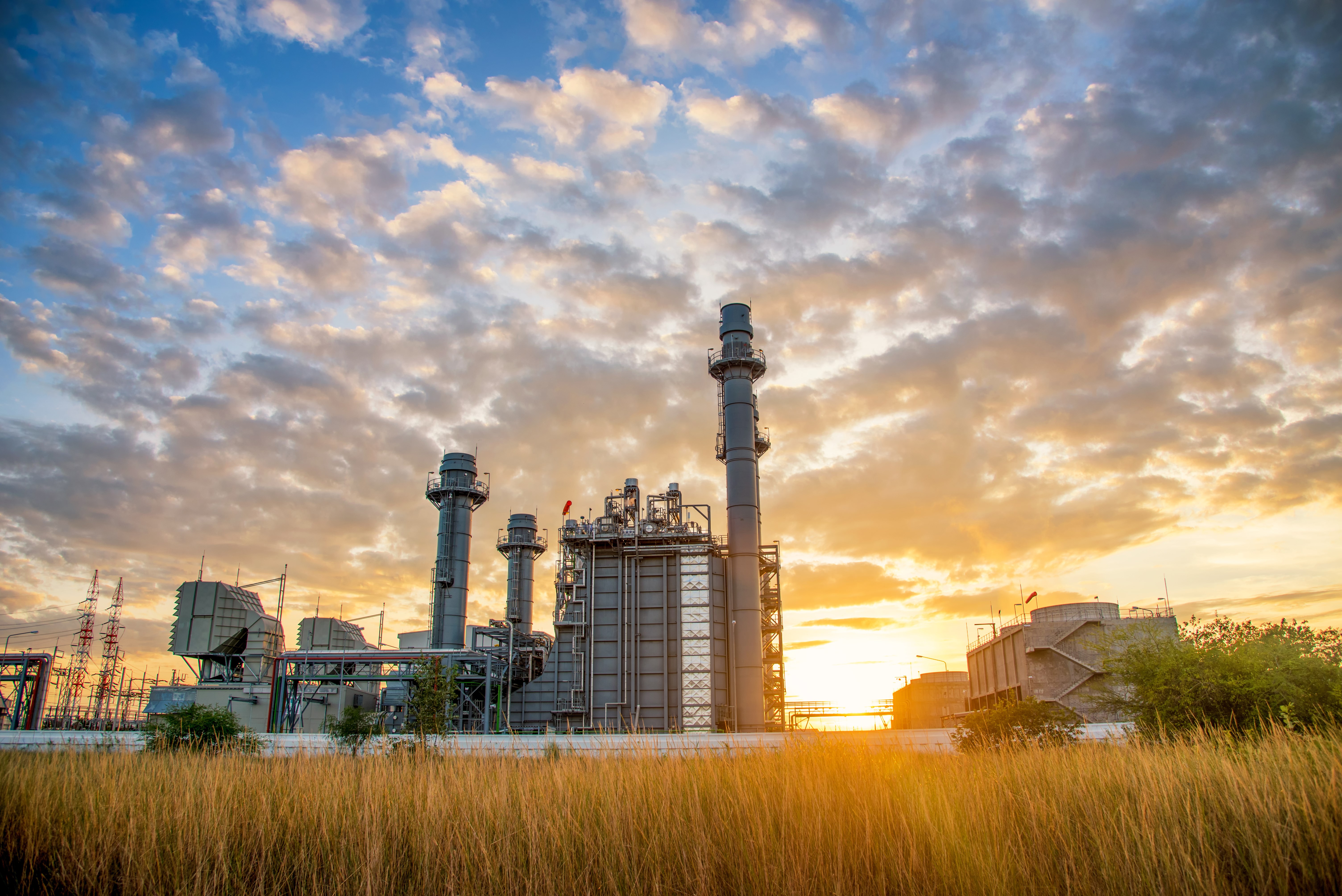
Condition monitoring solutions for the power industry
Considering the tough environmental demands of the power industry in general and the varying operating conditions in windmills in particular, SPM offers every piece of hardware and software equipment needed for an efficient condition monitoring solution, from the point of data collection all the way through to evaluated measurement data. On slowly rotating machinery, the SPM HD® measuring technique can be used with benefit. SPM HD uses RPM-based sampling frequency and algorithmic correlation techniques to ensure the highest possible signal quality and razor-sharp spectrums for analysis.
Portable instrumentation
Intellinova online systems
Condition monitoring in explosive environments
HD Technologies
Our wind farm solution
The purpose of condition monitoring is to maximize the lifetime profit of the plant by avoiding production losses and secondary damage incurred through the failure of vital parts, primarily the generator bearings, the gearbox, and the main bearings.
The SPM system is very sensitive and provides an early warning of a component’s deteriorating operating condition. This allows planned maintenance and replacements with the shortest possible downtime. Monitored parameters are shock pulses and vibration, the most reliable and specific condition indicators, at preset intervals. The system measures signal amplitudes, provides shock and vibration spectra, and, most importantly, individual values on specific fault symptoms showing the state of a bearing inner ring, a gearwheel, etc. The primary message that reaches the wind plant operator is an easy-to-understand condition value, coded green – good condition, yellow – alert, and red – bad condition, and a description of its most probable cause.
SPM provides reliable and easy-to-handle condition information, technically and economically adjusted to the requirements of each individual plant.

1. Generator
Recommended methods: SPM HD® and EVAM measurement of both shock pulses and vibrations.
Reason: Reduced bearing condition is the most common failure cause, together with misalignment.
Remark: Reliable, ample pre-warning time.
2. Gearbox
Recommended method: SPM HD® and EVAM
Reason: Coupling and gear-related problems on the high-speed side of the gearbox, shock pulse measurements for bearing condition on the slow rotating side of the gearbox.
Remark: Gearboxes are complex units requiring different measuring techniques to cover all faults. RPM is calculated from the rotor speed.
3. Main bearings
Recommended methods: SPM HD®, spectrum, and time signal analysis.
Reason: The proper method for slow-rotating bearings.
Remark: The RPM measurement is very important for slow-rotating parts.
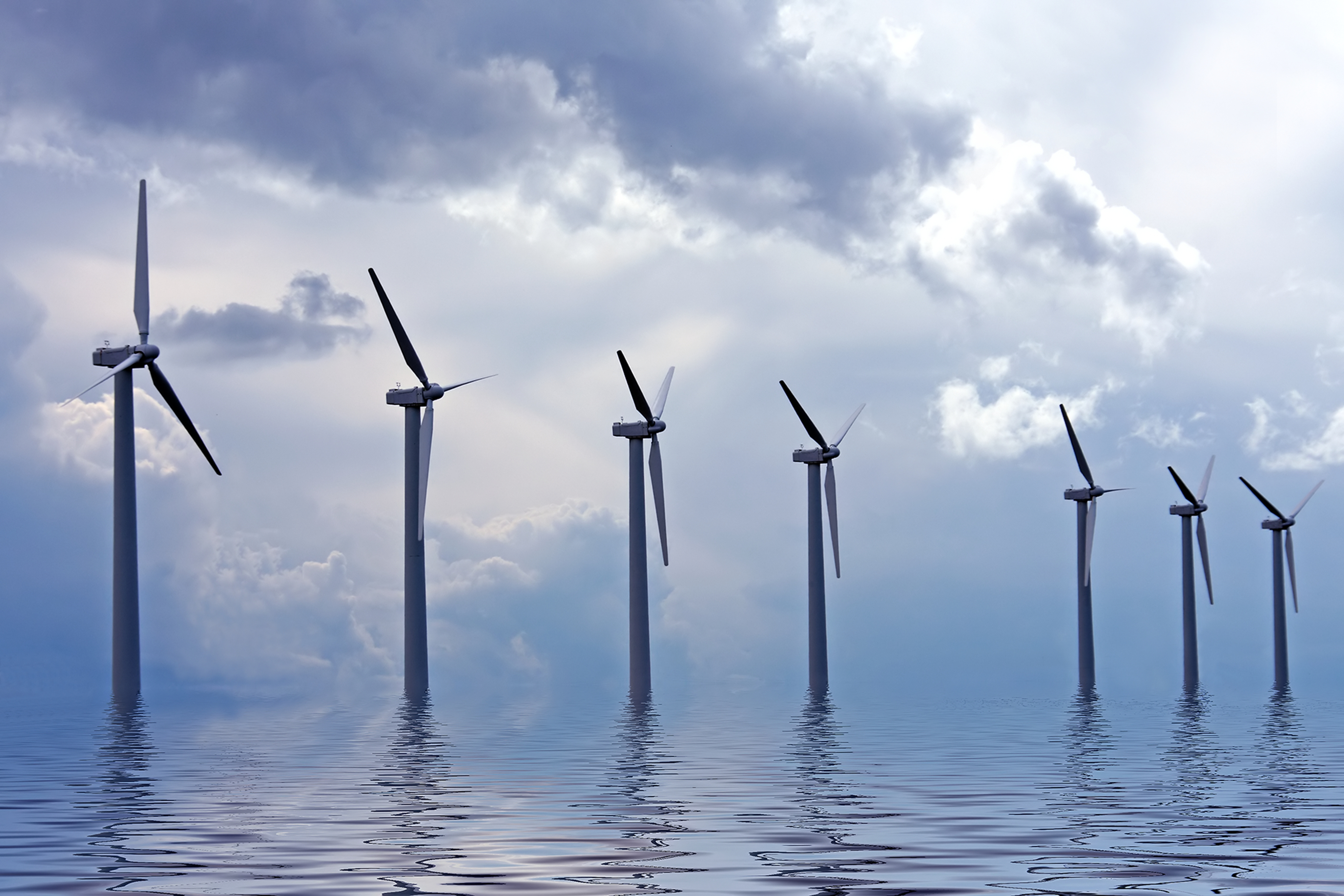
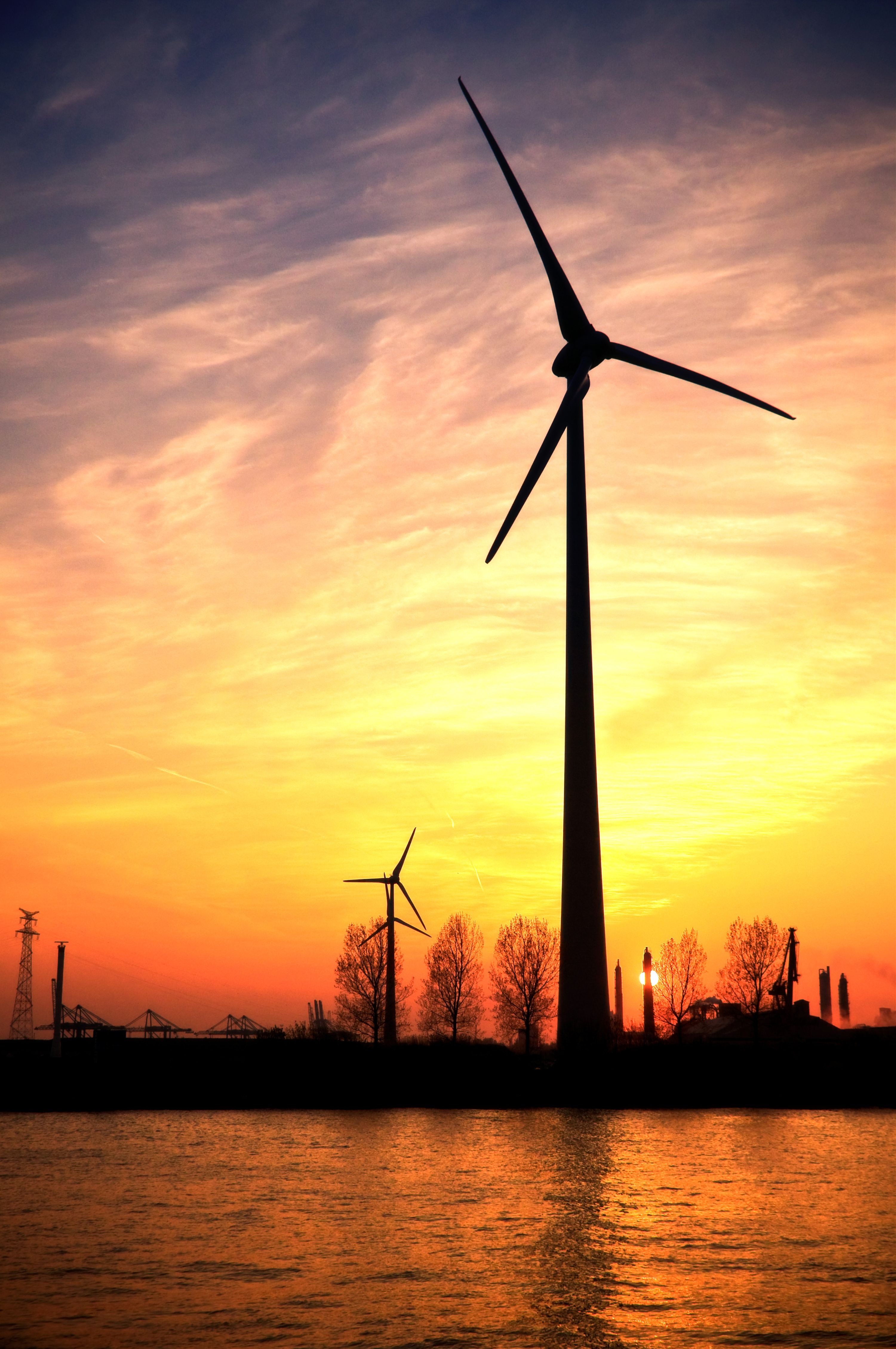